The core strength of the intelligent warehousing system-overall solution
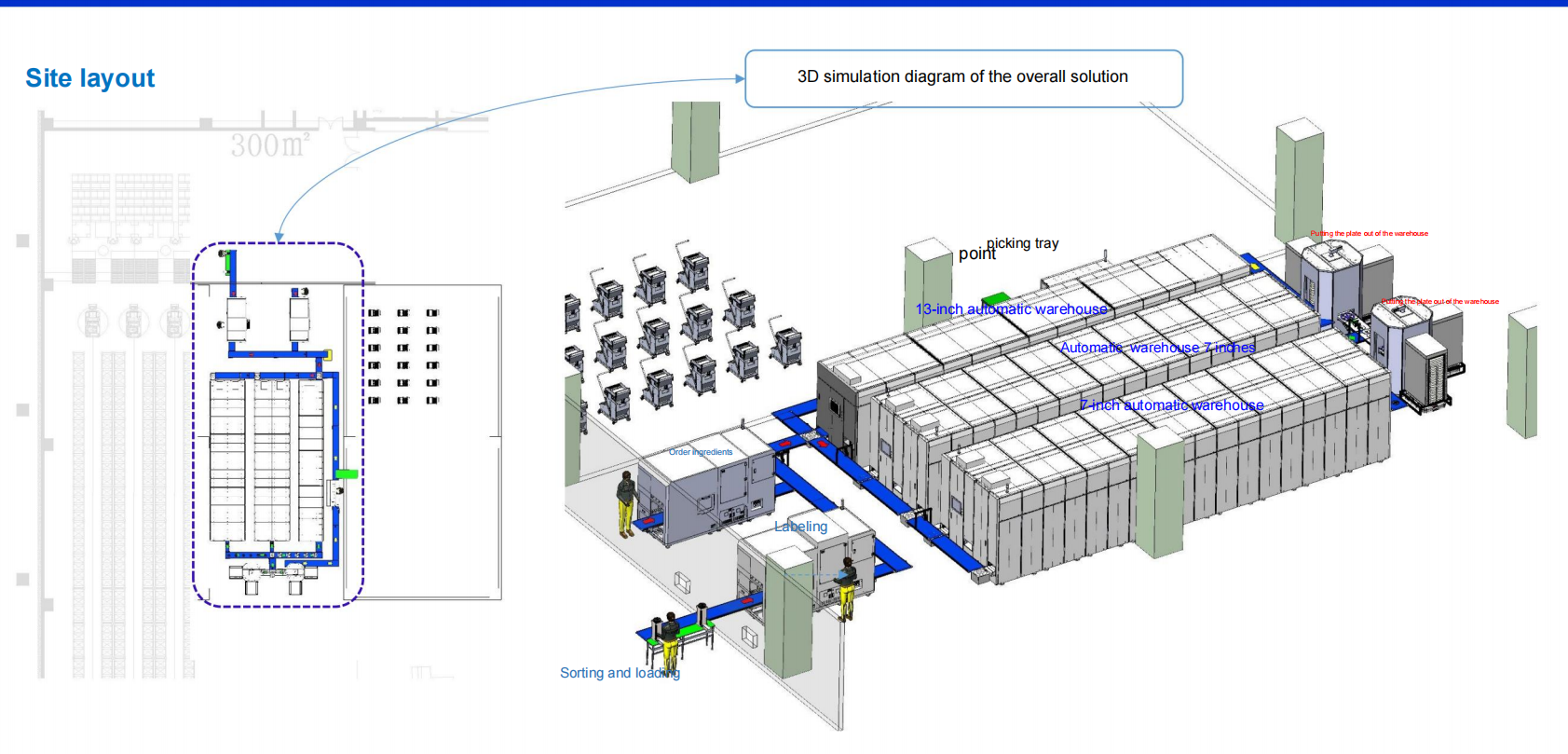
Core strength of intelligent warehousing system – overall solution – 3D animation
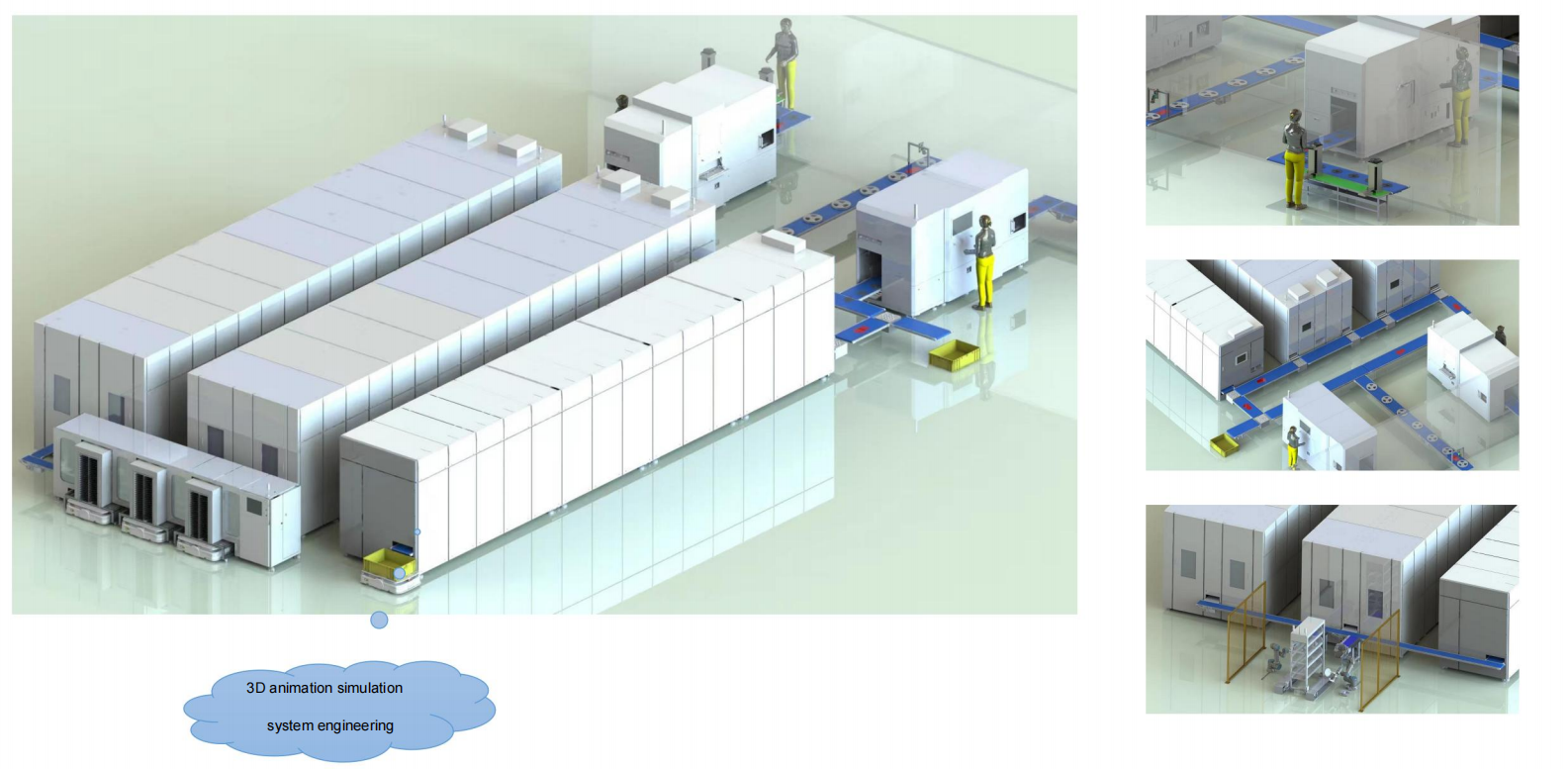
SMD Automated Storage Series: The Core Strength of Intelligent Warehousing System – Overall Solution
1. Introduction
In the fast-paced world of electronics manufacturing, the demand for agility, precision, and efficiency in Surface-Mount Technology (SMT) operations is at an all-time high. Traditional manual handling methods of SMD components are no longer sufficient to meet the demands of modern high-mix, high-speed production lines.
The SMD Automated Storage Series emerges as a strategic solution to transform passive warehousing into an active, intelligent logistics system. By combining hardware automation with software intelligence, this system becomes the core strength of a fully integrated intelligent warehouse.
2. What Is SMD Automated Storage?
The SMD Automated Storage Series is a smart, modular, and scalable storage solution designed specifically for storing and managing SMT reels, IC trays, JEDEC trays, feeders, and other surface-mount components. It is built to support:
- Fully automated loading/unloading of reels
- Barcode-based inventory management
- Environment control (temperature, humidity)
- Seamless integration with MES/ERP systems
- Real-time data reporting and analytics
This system eliminates manual intervention, dramatically improves traceability, and allows just-in-time (JIT) delivery to SMT lines.
3. Core Components of the System
3.1. Intelligent Storage Units
- Modular silos or towers, capable of storing up to 10,000 reels
- Dual or single-track robotic arms for high-speed access
- Supports multiple reel sizes (7”/13”, 8mm/12mm)
- Anti-static design and dust-proof sealed compartments
3.2. Central Control Software
- Real-time inventory monitoring
- FIFO material dispatch algorithm
- Smart BOM matching
- Alarm/exception notifications
- Visual dashboard and reporting
3.3. MES/ERP Connectivity
- Open interface for full integration with production systems
- Real-time data sharing on material usage, storage capacity, and location
3.4. Auxiliary Equipment (Optional)
- Barcode scanning and label printers
- SMT reel drying cabinets with nitrogen supply
- AGV/AMR smart transport integration
- Intelligent loading/unloading conveyors
4. Strategic Advantages of the System
✅ Zero Human Error
- Automated barcode reading ensures correct reel is stored or retrieved
- Prevents mixing of components or wrong part delivery to production
✅ Accelerated Line Changeover
- Grouped reel delivery allows SMT line to change product models quickly
- 50+ reels can be dispatched in one operation
✅ Maximum Space Utilization
- Vertical design makes the most of factory height
- Silo layout customizable to plant architecture
✅ Real-time Traceability
- Each operation (inbound/outbound) is time-stamped and logged
- Instant location tracking of any part in the system
✅ BOM-driven Operation
- Pick lists are generated based on the production BOM
- Reduces manual searching and ensures only relevant reels are retrieved
5. The Overall Solution: From Storage to Production
The SMD Automated Storage Series is not just a storage system—it is the nerve center of a smart warehouse ecosystem. It forms a closed-loop intelligent material handling solution by integrating:
Stage | Function |
---|---|
Incoming Material Check | Barcode scanning, humidity drying, reel inspection |
Smart Storage | Automatic reel loading and classification |
Digital Inventory | Real-time stock updates, FIFO algorithms |
Automated Dispatch | Pick-list generation, route optimization |
SMT Line Feeding | Delivery via AGV or conveyor, matched to feeder positions |
Data Feedback | Usage tracking, replenishment warning, analytics |
This creates a seamless, digital, and fully visible material flow pipeline.
6. Applications and Industry Use Cases
The system is now widely deployed in:
- Mobile device and wearable electronics factories
- Automotive electronics production (e.g., ADAS, ECU, infotainment)
- Industrial automation module assembly lines
- Contract manufacturers (EMS/ODM) handling small-batch, frequent changeovers
7. Technical Flexibility and Customization
Feature | Details |
---|---|
Reel Types | 7”, 13”, 15”, 17”; paper/plastic, anti-static |
Component Compatibility | Resistors, capacitors, ICs, inductors, LEDs, connectors |
Storage Capacity | 2,000 to 10,000 reels (scalable) |
Environment Monitoring | Temperature, humidity (with log) |
Software Customization | Language UI, report types, integration protocols |
Physical Expansion | Modular silo linking, additional robotic arms |
8. The Value Proposition
Investing in the SMD Automated Storage Series provides measurable benefits:
Metric | Improvement |
---|---|
Labor cost | ↓ 60–80% |
Inventory error rate | ↓ 95% |
SMT line changeover time | ↓ 50–70% |
Space utilization | ↑ 30–50% |
Material dispatch time | ↓ 70% |
Component loss (damage/mix) | ↓ 99% |
9. Future-Proofing with AI and IoT
The platform is designed to evolve:
- AI-enabled prediction for component shortage and replenishment
- IoT sensor network for environmental and operational data feedback
- Cloud connectivity for remote monitoring and big data analysis
- Digital twin support for warehouse simulation and optimization
This positions the system as a future-ready solution for fully unmanned smart factories.
10. Conclusion
The SMD Automated Storage Series represents the foundation of the intelligent warehousing system. It brings together automation, intelligence, traceability, and integration into one holistic solution. As factories worldwide strive for higher efficiency and lower costs, this system proves to be the core strength that enables digital transformation in electronics manufacturing.
From chaos to control, from manual to intelligent — SMD storage is no longer just shelves, but the brain of your smart factory.