The powder coating booth is one of the main pieces of equipment for electrostatic powder spraying. Clean in the powder coating booth to keep the airflow smooth, thereby providing a clean working environment for the operator. (Usually set to 10g/m3). Besides, the dust collection room should be cleaned so that the powder is not easy to deposit in the room, thereby changing the color of the powder, and the powder coating ovens should have enough light to facilitate the spraying wor
Powder coating booth system composition:
- Powder coating booth, when the bottom of the powder coating spray booth is cleaned, the bottom air pipe is a circular arc transition, there is no dead corner, and the automatic valve structure and side
- The edge of the air knife is automatically cleaned to effectively prevent powder from accumulating in the powder coating spray booth and recover the powder in time to ensure that the bottom structure is uniform and clean, and there is no residue accumulation
- The powder feeding system of the cleaning system: connect with the large cyclone pipe to form negative pressure and save dust
Types of powder coating booths
- PP powder coating spray booth
- Fast color-changing powder spray booth
- Design of large-scale cyclone two-stage recovery powder coating system
- Powder Supply Center
- Electrostatic powder coating equipmen
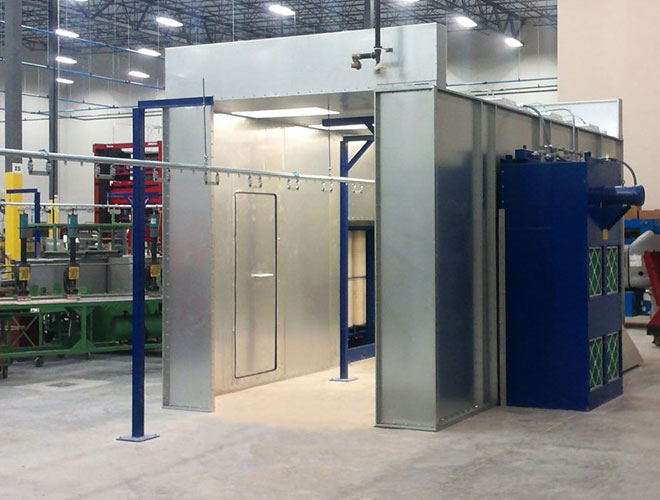
1. PP powder coating booth
PP powder coating booth
- Working method: manual spraying and automatic spraying
- Side panel, top panel: made of steel plate
- Bottom plate: made of steel with t = 3.0mm
- Powder recovery method: filter recovery
- Equipped with an automatic pulse backwash system, set up a pulse airflow automatic cleaning system
- Waste gas treatment method: intercept the waste gas filter and exhaust it indoors
- Automatic spray gun nozzle: 10 spray guns can be installed on one side
- Manual filling nozzle: 2 positions
- Benefit: lower cost
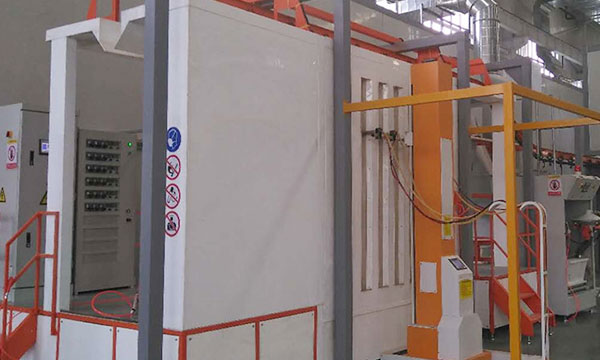
2. Fast color-changing powder coating booth
- A large cyclone two-stage recovery powder coating system
- High powder recovery efficiency and durable equipment
- The powder coating booth adopts
- PP engineering plastic board and the system is equipped with two manual spraying positions, which is convenient for workers to operate
- The large-scale cyclone separator adopts European technology, and the single separation rate can reach more than 96%
- The post-filter adopts a backwash filter for recovery, with high efficiency and low noise
- Equipped with automatic recovery and screening system to ensure the normal pollution-free circulation of powder
- The bottom of the powder coating spray booth adopts a baffle mechanism and a pulsed airflow automatic cleaning system to ensure timely recovery of overspray powder
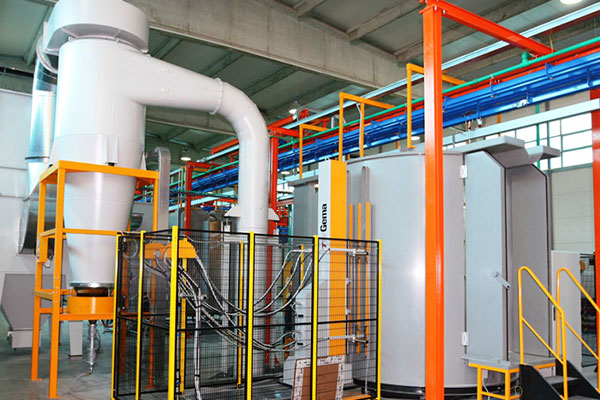
3. Design of large-scale cyclone two-stage recovery powder coating machine system
Large-scale cyclone two-stage recovery powder coating machine system
- Working principle: When spraying the workpiece in the powder coating oven, the excess spray powder is sucked away by a large amount of air by the fan. When using a specially designed recovery device and filtering system, the mixed powder in the air will be separated and filtered, thereby effectively recovering the powder and purifying the air.
- The spraying adopts electrostatic powder coat paint, the painting speed is fast, and the powder utilization rate is above 96%. The coating has excellent corrosion resistance, wear resistance, high adhesion, uniform coating, and edge thickness. Because there is no solvent, this method does not pollute the environment.
- Powder unrecovered device: This design uses a two-stage recovery system with a large cyclone dust collector and a powder core. The sprayed powder is collected by the cyclone separator and then enters the filter chamber for secondary recovery. The powder recovery rate can reach 96%.
Quick color change system function
The quick color change system is a new type of economical quick color change system. It takes about 15-30 minutes to clean the powder coating oven and complete the color change.
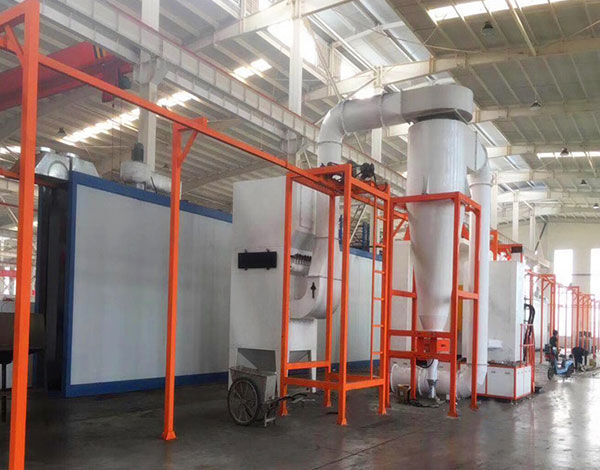
4. Powder Supply Center
The automatic powder supply center
The powder center is a compact powder supply system that can convey powder directly from the hopper. This special design is designed to quickly clean all parts of the powder to quickly change the color.
Powder feeding system: the maximum number1 of straws (up to 24), the lifting device of the straw unit, the automatic cleaning system of the straw, the powder level detector, the vibration platform of the powder collection bucket, and 2 fluidized powder buckets. The specially designed quick magic color change center (the powder pump bracket can be used to install 6-20 sets of spray guns), instead of the ordinary powder hopper for powder supply, has the following advantages:
- The vibrating screen is a continuous vibrating part. The frame has high strength and has a small gap, which is easy to leak. All of these are made by hydraulic molding. The 304# stainless steel housing is accurate in size and sealed.
- Automatic cleaning of all powder pumps, powder tubes, automatic cleaning, convenient and fast, only 10-20 minutes.
- The packaging cartons of the powder supplier can be used directly and can be easily used for small batch production.
- The recovered powder is directly connected to the cyclone separator system to avoid powder gas separation and save the powder.
- Use a sieve to remove the recovered powder impurities.
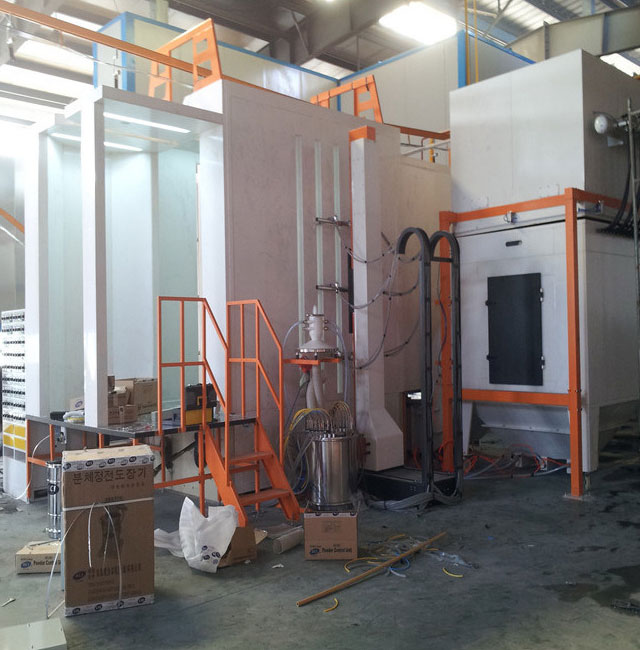
5. Electrostatic powder coating equipment
Automatic rubber powder recovery device
Powder coatings emit zero or close to zero chemical toxins (VOC). Compared with traditional liquid coatings, powder coatings can form thicker coatings without sagging or sagging. The over-sprayed powder coat spray is recycled, so you can achieve nearly 100% utilization of the coating. The powder coat spray production line is safer than the waste produced by conventional liquid coatings. The basic equipment and operating costs of any powder production line are usually lower than conventional liquid production lines. Compared with liquid-coated products, powder-coated products have fewer appearance changes between the horizontal coating surface and the vertical coating surface. A series of niche effects must be achieved, which cannot be achieved by other coating processes.
Powder coating paint system
• Spray pretreatment system
Treatment process: degreasing → washing → pickling and rust removal → washing → surface treatment → oxidation → washing → passivation → washing → drying
Purpose: Remove oil, dust, and rust on the top of the working surface, and deliver a corrosion-resistant layer, while increasing the adhesion of the coating.
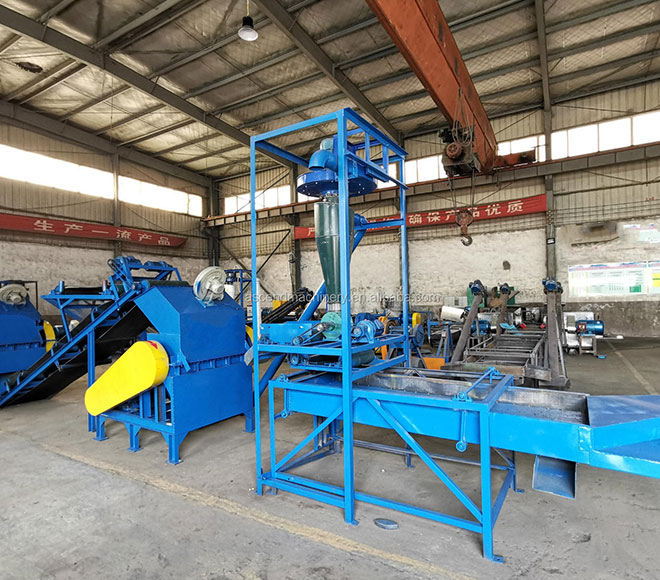
• Electrostatic painting
Purpose: Spray the powder coating evenly on the top of the working surface. Special working surfaces (including positions prone to electrostatic shielding) should be sprayed with a high-performance electrostatic sprayer.
Coloring process steps: Using the principle of electrostatic adsorption, a layer of powder coating is sprayed uniformly on the top of the working surface, and the powder is recovered by the recycling system, and it can be used after sieving.
• High-temperature curing
Purpose: Heat the top of the powder coating on the working surface to the specified temperature and corresponding time to ensure melting, leveling, and curing, so we hope that the working surface has an effect.
• Decorative treatment
Purpose: Help the work surface after electrostatic spraying to achieve unique appearance effects, such as various textures, patterns, light, etc. Processing steps: covering optical transmission and other processing technologies.
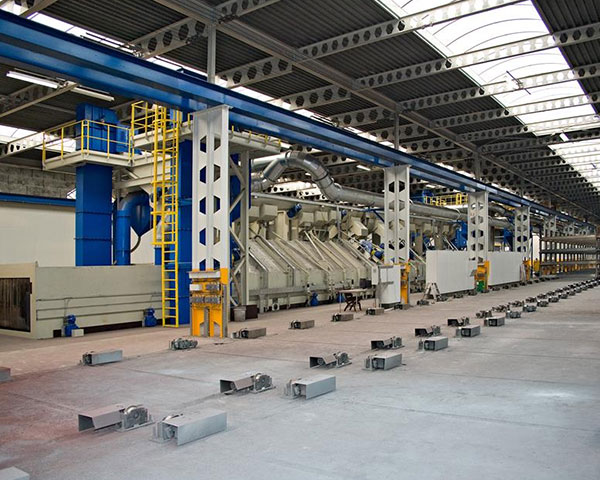