How Vertical Lift Modules Work: A Complete Guide
Introduction to Vertical Lift Modules
In today’s fast-paced business environment, efficiency and productivity are paramount. One technology that has revolutionized storage and inventory management is the Vertical Lift Module (VLM). But what exactly is a VLM, and how does it work? In this comprehensive guide, we’ll explore the inner workings of a VLM, its key components, and the benefits it offers to various industries.
Key Components of a Vertical Lift Module
A VLM is made up of several crucial components that work together to optimize storage and retrieval processes. Let’s take a closer look at each one.
Trays

Trays are the primary storage units within a VLM. They come in different sizes and can be configured to accommodate a wide range of items, from small parts to large and bulky goods.
Lift Mechanism

The lift mechanism, often driven by an electric motor, is responsible for moving trays vertically within the VLM. This enables the efficient storage and retrieval of items.
Control System
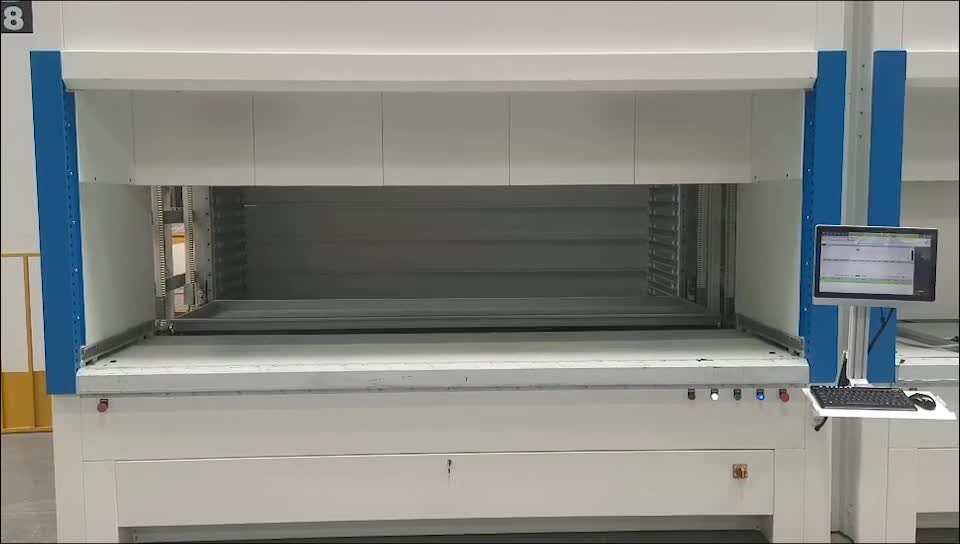
The control system is the brain of the VLM. It receives input from the operator, manages the lift mechanism, and ensures the smooth and accurate movement of trays.
The Working Principle of a Vertical Lift Module
Storing and Retrieving Items
The primary function of a VLM is to store and retrieve items. When an operator inputs a request, the control system directs the lift mechanism to move to the appropriate tray location. The lift then retrieves or stores the tray, bringing it to the access opening for the operator to load or unload items.
Automatic Tray Height Measurement
Modern VLMs feature automatic tray height measurement, which optimizes the storage space within the unit. The system measures the height of each item and adjusts the tray positions accordingly, minimizing wasted space and maximizing storage density.
Benefits of Using Vertical Lift Modules
There are several advantages to using VLMs in your storage and inventory management processes, including:
Space Optimization
VLMs make use of vertical space, allowing for significant storage capacity within a small footprint. This reduces the need for additional floor space and can even free up valuable square footage for other business operations.
Increased Productivity
By automating storage and retrieval tasks, VLMs reduce the time spent on manual processes, such as searching for items or walking between storage locations. This translates into increased productivity and efficiency for your workforce.
Enhanced Inventory Control**
VLMs are equipped with advanced inventory control features, such as barcode scanning and real-time inventory tracking. This allows for better visibility and management of your inventory, reducing the risk of stockouts or overstocking.
Improved Worker Safety
By eliminating the need for workers to climb ladders or operate forklifts, VLMs significantly reduce the risk of workplace accidents. Additionally, ergonomic design features, such as adjustable tray heights, help minimize the physical strain on operators.
Applications of Vertical Lift Modules
VLMs have found their way into a variety of industries, thanks to their versatile and efficient nature. Some of the most common applications include:
Warehousing and Distribution
In warehousing and distribution centers, VLMs can be used to store and manage a wide range of products, from consumer goods to industrial parts. They help optimize storage space, streamline order fulfillment, and improve overall operational efficiency.
Manufacturing
In manufacturing environments, VLMs are ideal for storing and managing raw materials, components, and finished products. They help reduce production lead times, minimize work-in-process inventory, and ensure that the right parts are always available when needed.
Retail
Retailers can benefit from the space-saving capabilities of VLMs by using them to store and manage inventory in backroom areas or even on the sales floor. This can help optimize the use of available space, improve stock management, and increase overall store efficiency.
Healthcare
In healthcare settings, VLMs can be used to store and manage medical supplies, pharmaceuticals, and patient records. They help ensure that critical items are readily available while maintaining a secure and controlled environment.
Choosing the Right Vertical Lift Module
When considering a VLM for your business, it’s essential to evaluate factors such as the size and weight of the items you need to store, the available space in your facility, and the required throughput capacity. Additionally, consider the level of integration with your existing inventory management systems and the level of customization required to meet your specific storage needs.
Conclusion
Vertical Lift Modules have transformed the way businesses manage their storage and inventory processes. By optimizing space usage, improving productivity, enhancing inventory control, and ensuring worker safety, VLMs offer a myriad of benefits to various industries. By understanding how VLMs work and considering the factors mentioned above, you can make an informed decision about implementing this innovative technology in your business.
FAQs
- What is the weight capacity of a typical Vertical Lift Module?
The weight capacity of a VLM depends on its specific design and configuration. Some VLMs can hold up to several thousand pounds per tray, while others may have lower weight limits. It’s important to choose a VLM that can accommodate the weight of your stored items.
- Can Vertical Lift Modules be used in cold storage environments?
Yes, certain VLMs are specifically designed for use in cold storage environments, such as refrigerated warehouses or food processing facilities. These VLMs feature insulated components and specialized materials that can withstand low temperatures.
- Are Vertical Lift Modules safe to use around people?
VLMs are designed with numerous safety features, such as access gates, safety sensors, and emergency stop buttons. These features help ensure the safe operation of the VLM and reduce the risk of accidents involving workers.
- Can Vertical Lift Modules be integrated with other warehouse management systems?
Many VLMs are compatible with warehouse management systems (WMS) and other inventory control software. This integration allows for seamless data exchange, providing real-time inventory updates and ensuring efficient order processing.
- How much maintenance do Vertical Lift Modules require?
While VLMs are designed for low maintenance and long-term reliability, regular maintenance is still necessary to ensure optimal performance. This typically includes routine inspections, lubrication of moving parts, and periodic checks of electrical components. Following the manufacturer’s recommended maintenance schedule can help prolong the life of your VLM and minimize potential downtime.