With the development of the global economy, automated warehouses have gradually replaced traditional storage shelves and gradually become the mainstream storage system in today’s warehousing industry. So So how to design and install an automated warehouse? In this post, we will break down the key points of the design and installation of Automated Storage System!
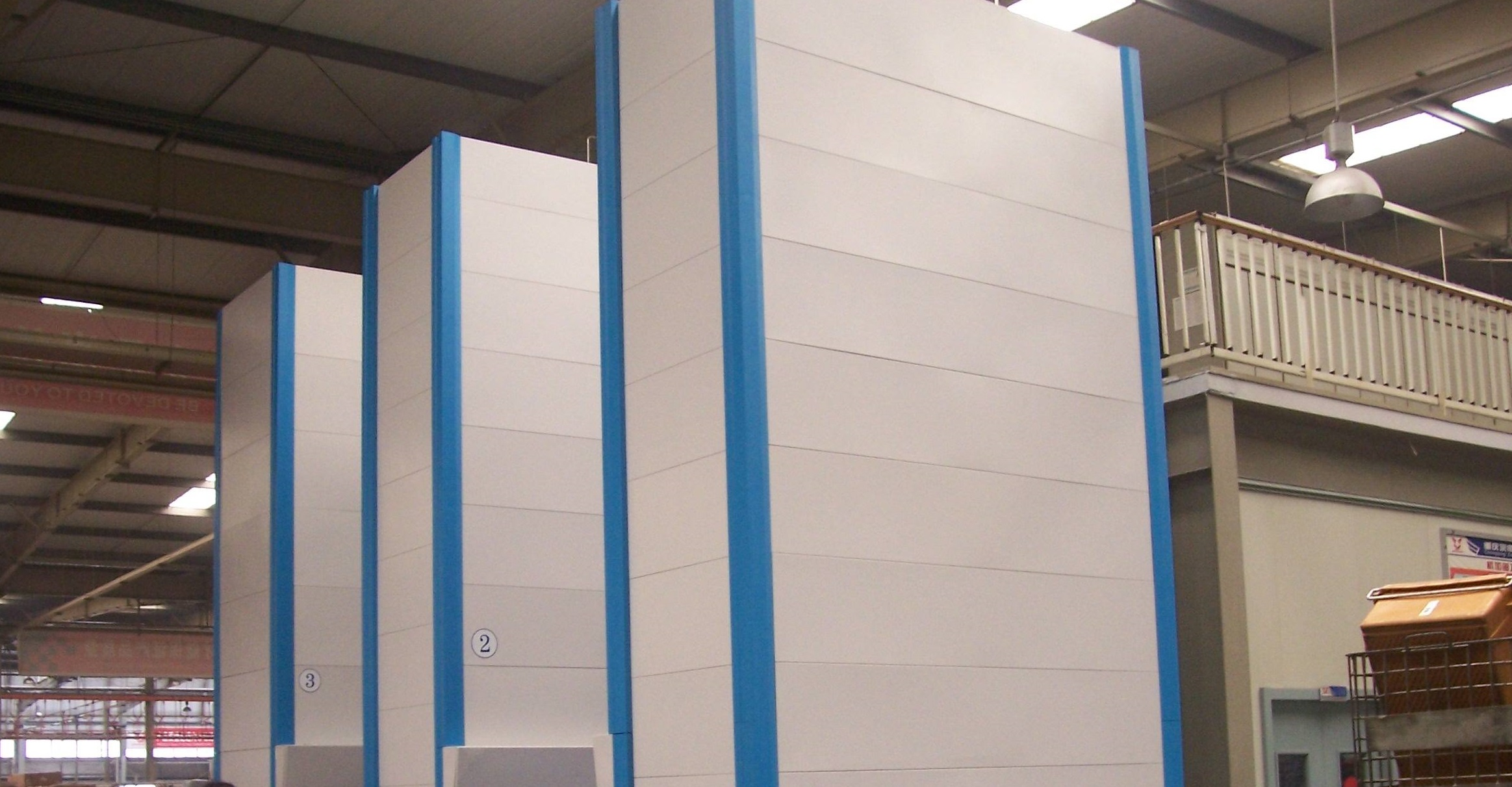
1. Key Points of Automated Storage System Design
Now what we call an automated three-dimensional warehouse or automated storage system, its content has greatly exceeded the previous definition. Simple classification, including Pallet Lift Modules (AS/RS) and vertical carousels (Miniload). Under the two, there are many subclasses, such as:
- AS/RS: Single-depth stereo carousel, double-depth vertical carousels, storage lifts, dense storage system (there are many forms), etc. In addition, there are different forms of pallets, different forms of shelves, different forms of rails, different forms of control, and different forms of stacker structure, etc., which are decomposed into many subcategories;
- Miniload: single depth, double depth, multi-level shuttle system, 4-way shuttle system, etc.
There are many types and forms of further subdivision. For simplicity, I will not list them all here. The following descriptions are also based on simple AS/RS, and occasionally talk about other content.
The main equipment and ASRS systems that constitute a automated warehouse include: racking system (shelf, roadway equipment, platform, etc.), stacker system, conveyor system, pallet, network and information system. In addition, there are supporting forklifts, signs, guardrails, etc.
From the designer’s point of view, the automated warehouse may only be a part of a logistics system. At this time, the overall location and supporting systems should be considered, including the receiving system, the delivery system, the storage area, the picking area, the packaging area, and the sorting area. District, etc. Of course, the choice of storage format is critical.
- Stacker (AS/RS): As one of the key equipment of the three-dimensional warehouse, the stacker is very important. The process should be reasonable, the brand and model of the motor and reducer should meet the requirements, the safety measures should be comprehensive, and the positioning method should meet the requirements. The installation inspection of the stacker is a very professional work. As an installation inspection, the focus should also be inspected and tested one by one in appearance inspection, main component models, safety protection devices, equipment function demonstration, speed, positioning method, positioning accuracy, operating ability, noise and other aspects.
- Conveyor: To meet the overall design requirements. Including surface technology, motor and control system, safety measures, etc. The installation inspection includes inspection of the installation appearance, whether the surface of the roller table is flat, whether the main components meet the requirements, and whether the equipment functions are complete.
- Tray: meet the design requirements, including overall size and plate thickness. In addition, the bearing experiment should meet the requirements. Although the pallet is simple, the quantity is large. It is not easy to make each pallet meet the requirements. The pallet has a great impact on the normal operation of the automated storage system.
Single depth or double depth: There are not many cases of double depth, and there are many restrictions on double depth in addition to the inventory increase of about 15 to 25% in certain cases. Some designers relish the use of dual-depth stereoscopic carousels, which often fail to achieve their goals without accurate analysis.
When choosing what technology to use, the key metrics are inventory, efficiency and cost. These three indicators are not absolute. Sometimes inventory requirements are high and efficiency is not an issue; sometimes efficiency and cost are key. Also, consider applicability.
The following are key to the design phase:
(1) Basic data
The design is based on the underlying data. Any design, without the basic data is meaningless, can not judge the merits of the design. Many designers don’t understand this, draw a picture as soon as they come up, and the result is useless.
The most critical of the basic data are inventory, receipt and shipment volume, zeroing volume, working hours, SKU quantity, etc. Generally, these data should be used as a reference for historical data or peer data. The more accurate the underlying data, the more rational the design.
(2) Load
The bearing capacity of the foundation (including ground and floor): should be calculated according to the specification, not arbitrarily determined.
Shelf carrying capacity (seismic load is the focus): It is necessary to use the finite element method for mechanical analysis, especially the determination of seismic load, which is very critical.
(3) Floor height
There are several concepts of floor height, such as floor height, the height of each floor of the shelf, etc., here only refers to the height of the shelf.
The layers are simple, and for a novice or non-professional, it is often error-prone. For a single-depth stacker, the floor height includes beam h1, pallet h2, cargo h3, access space h4, safety space h5, in addition to the bottom height and top height. Determining the layer height is not an easy task without an in-depth understanding of the stacker. For double depth, there are more complicated regulations for layer height.
It should also be noted that combined shelves generally have a fixed pitch limit.
(4) Warehouse front area and warehouse rear area
To determine the size of the front and rear areas of the warehouse, we must first have a full understanding of the structure of the stacker. Many people are confused about this. If you are an inexperienced designer, it is best to refer to other people’s designs. Correctly understand the front and rear areas of the warehouse, and also understand the requirements of the maintenance area.
(5) Efficiency
The efficiency of the stacker can be calculated, and the calculation method is given in the FEM9.851 standard. But for double depth, the calculation is a little more complicated.
Efficiency of stacker cranes is a key factor, but it is not easy to get the right idea of how to improve efficiency. Some designers are inexperienced and tend to focus only on one indicator while ignoring others. Sometimes the results of calculations are often unexpected.
(6) Conveying system
As a peripheral supporting facility, the design of the conveyor is often more important and complex than the three-dimensional warehouse itself, and its difficulty is also greater. There are many technologies used in conveyors. In addition to traditional conveyors, shuttles, circular shuttles, AGVs, etc. are widely used now. No matter what technology and equipment are used, its application and technical requirements must be clearly understood.
The design of the conveyor system also considers the matching of efficiency. Sometimes, what kind of conveying form and conveying speed are used has a great influence on the efficiency of the conveying system.
(7) Fire zoning issues
The fire division has a great influence on the design of the automated carousel. For Class II materials, the partition area with automatic spraying is 3,000 square meters, while a fully automatic warehouse is limited to 12,000 square meters. This is one of the reasons why the automated carousel modules cannot be built very large. In the design stage, how to make full use of fire codes is very important.
There are many design parameters of the vertical carousel. As a professional designer, the most important thing is to be balanced and applicable. Balance is that all design indicators should be consistent, and some indicators should not be too high and some too low. Too high indicators will cause waste, too low indicators will affect the ability of the entire system, which is also a waste. To apply means that the technology used is appropriate, not to apply for the sake of application. The initial designers did not know much about the application of the automated carousel, and there were many cases of misuse. Tailor-made, according to local conditions, in order to be appropriate.
2. Key Points of Automated Storage System Warehouse Design Installation
From an integrator’s point of view, a lot of equipment needs to be purchased, and only part of the equipment needs to be produced by itself. Whether it is purchased or produced by ourselves, the quality requirements are the same.
Shelf system: First of all, the shelf must be calculated by mechanical finite element, the structure must be reasonable, the technological level must meet the requirements, the thickness of the surface coating must meet the requirements, the color should be uniform, and the processing accuracy must meet the specifications. From the buyer’s point of view, the materials (mainly columns and beams) must meet the requirements. How can I be sure that the material meets the requirements? In addition to the identification of the purchase order, important items also need to test the physical properties of the material. In addition, the installation of the shelves is very important. In addition to the installation according to the design requirements, the installation results should be checked.
The more important installation issues are as follows:
(1) Foundation pre-buried problem
In many cases, the pre-embedded foundation does not meet the requirements. In addition to supervision and guidance during the installation process, it seems to be a more economical way to find problems and correct them in time. Once reworked, the quality is often unsatisfactory, the cost will increase, and the construction period will be extended.
(2) Installation reference
The installation benchmark of the shelf is very important. It is necessary to determine the benchmark during construction. At present, many domestic projects have not done this, resulting in some problems.
(3) Safety pin
An easily overlooked issue is the safety pin of the beam. Many accidents are also caused by safety pins. In addition, it is not uncommon to see problems with the height of the front and rear beams. Therefore, at the end of the installation, it is very necessary to carefully check the safety pin and beam height. Installers should develop good habits and avoid unnecessary mistakes.
(4) Track connection
Track connection is an important issue in installation. Many poorly connected tracks not only affect the use, but also have hidden dangers of breakage in the future.
(5) Ground
The shelves are required to be grounded to prevent electrostatic damage to the equipment. This is also very important.