Powder coating spray booth production is a key process in the spraying production process, the key to the surface quality of the sprayed profile lies in the control of the various process parameters in the spraying process. The amount of powder and atomised air are two key technical indicators, before the formal spraying of powder, you can try spraying a few times, when you can observe the size of the amount of powder and the uniformity of powder distribution at both ends of the spray booth. At this time the powder in the distance from the end of the gun within 10cm-15cm part of the straight line running, outside the part is to atomised powder form, adsorbed on the surface of the profile is in fact this atomised effect of the powder, whether the existence of this atomised effect of the powder is used as a standard to control the distance between the gun and the profile. In addition to the process parameters, some of the necessary small aspects should also be noted.
1. Position of the spray gun
The spray gun should be kept at a certain inclination, biased in the direction of the profile running, the gun should be kept vertically parallel in the arrangement, the end part should be kept in a straight line, there should be no overlapping part between the guns, the upper and lower guns should be positioned so that the powder covers all the profiles.
2. Control of fluidised air pressure
The role of fluidised bed is to use the role of airflow, so that the powder forms a proper fluidised state, feel similar to the state of liquid flow, detect fluidisation to reach the full state, the simplest operation is: when stirring the powder by hand or stick, the presence of resistance is not felt. Fluidisation facilitates the powder to be drawn into the conduit, under the action of accelerating wind, to produce the effect of atomisation, insufficient pressure or too much pressure will cause insufficient fluidisation to be produced.
3. Recycling of the powder
Absorbed powder on the surface of the profile only accounts for about 1/3 of all the powder from the gun, scattered in the spray booth more powder, recycled powder must be mixed with the new added powder in the appropriate proportion, the effect is better, so the powder should be recycled and reused in a timely manner.
4. The closed spray booth
The powder is easily polluted by the suspended matter of the outside air, and the surface of the profile is prone to flocculation or shrinkage after powder spraying, which affects the flatness of the surface of the profile after baking, so the spray booth should take closed measures to prevent the invasion of pollutants. The residual powder in the air pipe should be cleaned and cleansed in time. If the powder is not used for a long time, it will be easily caked and the powder will easily produce the phenomenon of spitting powder, which will affect the spraying effect.
5. Spare powder bucket and fill powder
Spare powder bucket, in order to be used when changing powder, can effectively improve labour efficiency, spare powder bucket dust, moisture and other maintenance work must be done to ensure the quality of the remaining powder in the bucket. In addition, the work of powder replenishment should also be paid attention to, although the technical parameters have been debugged before the normal production, but also through the powder replenishment window from time to time to carry out uninterrupted monitoring of the profile, found that the powder shallow and not adsorbed powder place timely replenishment powder. As the amount of powder ejected by the manual friction gun is larger than that of the automatic gun, the manual friction gun can be swung by hand at an appropriate speed.
6. The production process of the oven should pay attention to the problem
The production process of the oven should pay attention to the problems, powder coating production process, due to the limitations of the production line, resulting in the running time of the profile in the oven that completes the entire baking process, although the oven is relatively simple in terms of operating procedures, but in the process parameters control requirements are relatively strict, such as the running speed of the conveyor belt, furnace temperature control, running speed can be controlled by adjusting the frequency of the frequency conversion motor, furnace temperature The key point involved in the control is the adjustment of the gas supply pressure, which is required to be stable at around 1kg/cm2. To achieve this, pipeline gas is generally used, and the pressure supply pressure is constantly adjusted using a pressuriser to ensure the normal operation of the combustion unit.
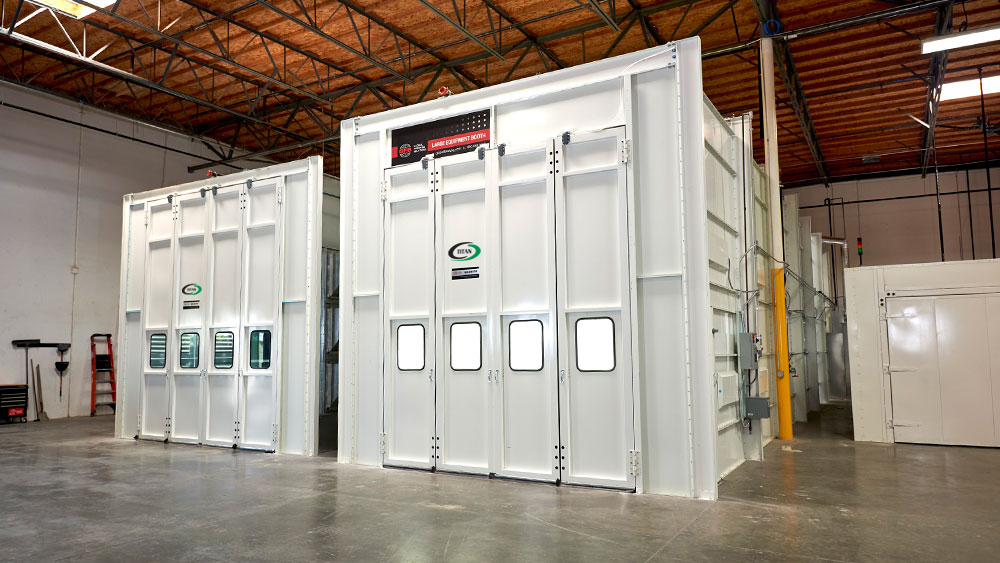