The establishment and maintenance of a company’s competitive advantage must be guaranteed by efficient and reliable logistics operations. Adopt effective material storage management, and establish a fully intelligent and automated modern material storage system to improve the core competitiveness of enterprises with half the effort. KENWEI effectively applies information technology for enterprises to improve management level and work efficiency, to meet the needs of the material supply system of “unified command, rapid response, and efficient operation”, in accordance with the requirements of modern warehouse management, to create a set of internet of things technology to fully promote the intelligent warehousing work of the modern intelligent warehousing system. The use of RFID intelligent storage management systems will optimize and intelligently manage all logistics links of enterprises, which can greatly reduce the cost of enterprises and enhance their competitiveness.
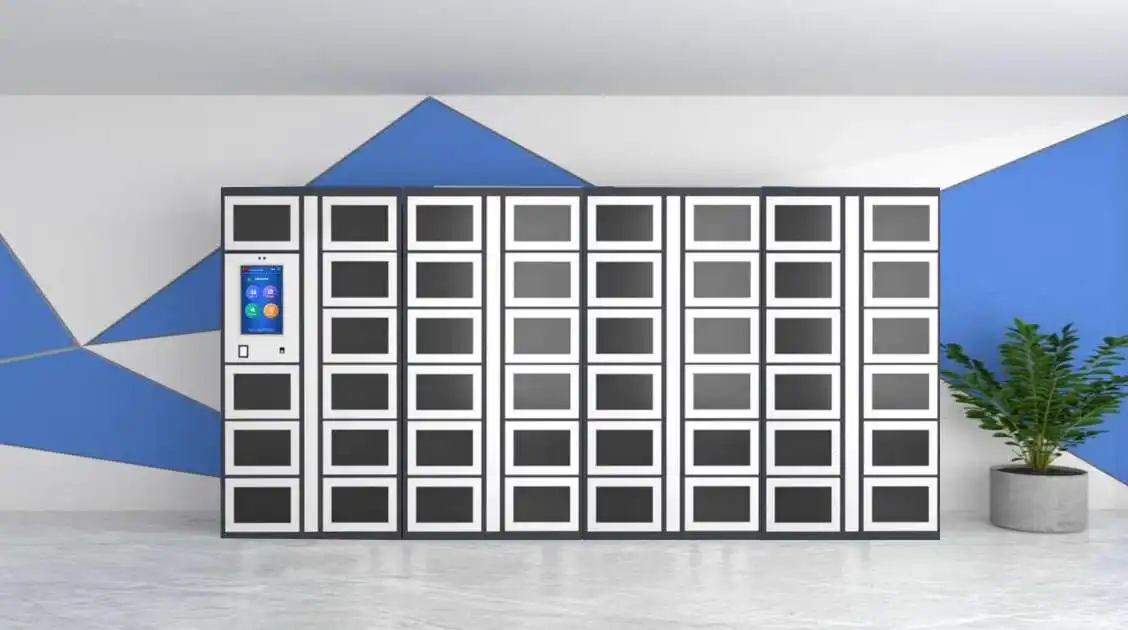
RFID Intelligent Storage System Composition
The RFID intelligent storage management system highlights the coordination of warehousing and information flow, with warehousing as the entry point, enabled by the Internet of Things technology based on intelligent dense warehousing systems, wifi real-time wireless transmission technology, RFID automatic identification technology, and video, intelligent electronic kanban board, on-site PDA scheduling system, and material scheduling platform software composed of material scheduling platform system.
RFID intelligent storage management system process:
- 1. Acceptance of arrival
- 2. Sampling test
- 3. New purchase, return and exchange into the warehouse
- 4. Delivery out of the warehouse
- 5. Specify the outbound batch return
- 6. Return and exchange of goods
RFID Automatic Retrieval System
Intelligent warehousing, automatic transportation, in and out of the warehouse control all rely on the identification and positioning of equipment and materials, of which, the speed, method, and accuracy of identification is the key. The application of RFID electronic tags, in the group identification link has played an important role. The system mainly consists of three components: composite label, composite label production system, RFID group identification system. The RFID group identification system is fixedly installed at the process demarcation point and completes the group reading, entry, identification, and confirmation functions, requiring accurate reading quantity, no missed reading, and the more group reading, the better. We customize the RF gate system, install the warehouse junction, and interface with the intelligent storage system to achieve the group entry function. Forklift material group identification: the forklift is modified, and RFID radio frequency devices and vehicle computers are installed on the forklift for automatic command and identification of on-board objects and feeding instructions. When the forklift forks up the material, the RFID radio frequency device installed on the forklift will automatically identify the pallet material information, and through the material information comparison of the material dispatching platform system, the driver is instructed on the on-board computer to operate the process and handling information.
Handheld radio frequency identification: the handheld support scanner, imager, RFID module, wireless LAN and wireless WAN RF through the handheld group identification of warehouse materials, inventory of materials. At the same time, through the Wifi network real-time and material dispatch platform system connection to obtain material inventory information and real-time tracking and verification of materials in and out of the warehouse.
RFID Intelligent Storage Management System Function
- 1. Warehouse management Warehousing management includes five core business systems of warehousing management, outbound management, inventory management, arrival management and supplier management.
- 2. Plan management According to the needs of the material depot, arrange the work plan, and track and record the implementation of the plan.
- 3. Linkage scheduling Order scheduling tasks through the information portal system, the central control room operation station and the on-site PDA.
- 4. Alarm management Display fault information on the central control room operation station and the electronic kanban board of the production site, including the time, duration, location, fault content, etc.; Alarms alert the operator by voice,
- 5. Comprehensive statistics Form comprehensive statistical reports based on various data such as inbound and outbound warehouses and distributions, such as monthly reports, annual reports, inventory reports, and provide detailed account inquiries for warehousing, inventory summary statistical reports, outbound summary statistical reports, and inventory classification summary statistical reports.
- 6. Decision analysis Based on the effective collection and accumulation of various data such as warehousing and distribution, the above data is extracted and mined to form an effective data support for the macro operation of material scheduling and material management, KPIs, etc., and provides a basis for leaders to assist in decision-making through various visual analysis and display.
- 7. Asset management The main assets and equipment of the material warehouse (warehouse, conveyor line), etc., as well as the asset information of storage materials, equipment and other equipment, are managed.
RIFD ASRS System Features
- (1) The application of Wifi technology and PDA technology makes on-site mobile office and scheduling possible, customized on-site scheduling software, so that managers do not need to operate in front of the computer, can directly command on the spot, and can interact with the central control room information in real-time.
- (2) The application of Rfid technology enables the entry and exit of materials and equipment to achieve batch and non-contact primary identification, which accelerates the efficiency of materials in and out of the warehouse.
- (3) The use of an intelligent intensive storage system enables the in-and-out transportation and warehousing of materials to achieve fully automated transportation and storage and can realize the rational storage of inventory through intelligent scheduling.
- (4) The setting of the on-site intelligent electronic kanban and the center’s large-screen display system makes the operation of the equipment and business on the site clear at a glance, and the information issued by the center can also be sent to the scene and the center in real-time through the intelligent electronic kanban, so as to realize the functions of on-site online notification, training, publicity and so on.
- (5) The overall integration of the system, the system from design to construction are in accordance with the characteristics of warehouse management, to the purpose of information integration, the interface between each system is a standard interface, and the modular subsystem relies on a standard database, step-by-step implementation will not cause interface difficulties.
KENWEI is a high-tech enterprise focusing on R&D, production, sales, intelligent storage software and hardware development. Its main members focus on more than 15 years of experience in the field of intelligent storage, focusing on solving intelligent storage and integrating closed-loop management of people and things.